Operatie Made by Driessen geslaagd
Met een open huis en een feestelijke avond viert Driessen in Eersel op vrijdag 13 december niet alleen het 40-jarig bestaan. Deze bijzondere dag markeert ook het (voorlopige) einde van een ingrijpend verbetertraject dat zich de afgelopen twee jaren heeft voltrokken. Met Made by Driessen staat er nu een modern plaatbewerkingsbedrijf waarmee de eigenaren verwachten de komende 10 á 15 jaar verder te kunnen.
Hiervoor is de hele zaak op zijn kop gezet: twee bedrijven (Kempmetal en Driessen) zijn samengevoegd tot één bedrijf onder één dak, de productieruimte is volledig opnieuw ingericht om een optimaal logistiek proces te creëren en de kantoorruimten en kantine zijn volledig gerenoveerd. Tevens is geïnvesteerd in nieuwe machines en zijn tientallen oude machines van de hand gedaan.
Minutieus plan
Made by Driessen wordt geleid door de drie eigenaren: de broers Stefan en Dennis Driessen en Olaf Jansen. Stefan is verantwoordelijk voor de verkoop/marketing, Dennis voor de financiën, administratie en het personeel en Olaf voor de technische aansturing van het bedrijf. Terugkijkend op de afgelopen intensieve jaren kan het trio niet anders dan constateren dat de hele operatie super is gelukt. “Alles is conform een minutieus plan gefaseerd uitgevoerd. De verbouwing is per hal gegaan en we hadden alles uitbesteed. Productietechnisch hebben we er heel weinig last van gehad. We hebben er slechts één dag volledig uitgelegen.” Het verbetertraject vindt zijn oorsprong in 2016, toen Driessen investeerde in de eerste fiberlaser om de groei te kunnen bijbenen. Die groei was ook de aanleiding om alle zaken eens kritisch in ogenschouw te nemen. Stefan Driessen: “We deden op twee plekken (bij Kempmetal en Driessen) precies hetzelfde, de efficiency was soms ver te zoeken. In 2018 hebben we de knoop door gehakt en besloten alle plaatwerkactiviteiten verder onder één naam en één dak voort te zetten. Daarbij heeft SpartnerS Organisatieadvies een belangrijke rol gespeeld. Ook wij hebben hun befaamde vliegtuigjes zitten vouwen. Dat was echt een eyeopener. Toen hebben we gedacht: laten we eens kritisch naar onszelf kijken: wat willen we als plaatwerktoeleverancier, wat willen we maken, wat voor machines zijn daar voor nodig en waar moeten die dan staan.”
Alles klaar bij jubileum
Er werd een verbeterteam met negen mensen van zowel Kempmetal als Driessen opgezet, gesteund door SpartnerS. Zij stelden een lijst met grote en kleine verbeterpunten op, waarmee ze aan de slag gingen. Daarbij werd er direct een dag gepland waarop alles klaar moest zijn: 13 december 2019, de dag dat Driessen het 40-jarig bestaan viert. In de lange aanloop naar deze dag is er heel veel gebeurd. In zowel 2016 en 2018 zijn er twee nieuwe kantbanken en een fiberlaser geplaatst. In 2019 is het hele bedrijfspand gerenoveerd en heringericht. De kantoren zijn gerenoveerd met fonkelnieuwe werkplekken, de kantine is smaakvol opnieuw ingericht en in de productie zijn hagelnieuwe werkbanken en gereedschappen in gebruik genomen. Ook is een moderne klimaatinstallatie geïnstalleerd die de productieruimte koelt en verwarmt en de lasdampen afzuigt. 7.000 vierkante meter aan productieruimte is helemaal opengegooid. Alle machines – behalve de ponslasercombinatie – hebben een nieuwe plek gekregen om een zo logisch mogelijke routing te realiseren, welke met de nieuwe belijning mooi wordt weergegeven. Tientallen machines zijn afgevoerd naar de vestiging van Kempmetal en daar met hulp van Troostwijk Veilingen van de hand gedaan. Daarbij zijn rigoureuze keuzes gemaakt. Zo zijn een nog jonge laser (4×2 meter) en kantbank (4 meter) verkocht. Olaf Jansen: “Ooit wilden we met Kempmetal meer in het grote bereik gaan doen, maar daar hebben we nu bewust afscheid van genomen. Die grote machines pasten niet in onze nieuwe organisatie, namen te veel vierkante meters in beslag en de logistieke handling van grote platen zou een te grote belasting zijn. Die markt willen we niet aanboren.”
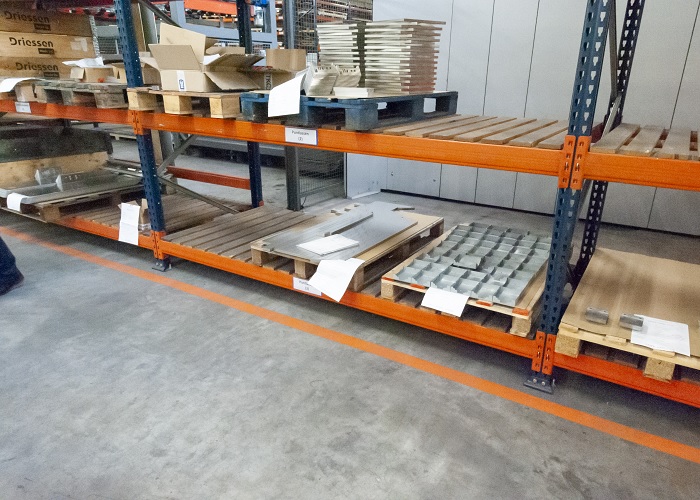
De werkplaats is ingericht volgens de 5S methodiek. Op alle rekken staan duidelijke aanduidingen, die aangeven waar wat moet liggen.
Nummer 1 plaatwerkleverancier
Welke markten wil Made by Driessen dan wel aanboren? “Wij richten ons helemaal op de productie van hoogwaardige dunne plaatdelen (0,5 tot 2 à 3 mm dik) en het daarbij zoveel mogelijk waarde toevoegen voor de klant”, zegt Stefan Driessen. “We willen de nummer 1 plaatwerkleverancier zijn in de regio qua nakomen van afspraken over kwaliteit, flexibiliteit en leverbetrouwbaarheid. Dat stralen we ook uit met ons nieuwe logo en onze nieuwe website. En met de tagline ‘Made by’, waarmee we aangeven: als het bij Driesen is gemaakt, weet je dat het goed is. De kleur oranje in onze nieuwe huisstijl sluit goed aan bij Holland High Tech, wat belangrijk is als we ook de grens overgaan.” Dennis Driessen vult aan: “We focussen continu op spreiding in ons klantenbestand en de branches waarvoor we werken: de machine- en apparatenbouw, land- en tuinbouwsector, medische en hightech industrie en auto-aanpassingen. Werk dat niet bij ons past, nemen we niet meer aan. Dat is een keiharde afspraak die we met ons drieën in het managementteam hebben gemaakt.”
Niemand hoeft meer te zoeken
Alle processen – te beginnen met de verkoop – zijn geoptimaliseerd, waarbij de veranderingen in de productie natuurlijk het meest in het oog springen. De werkplaats is ingericht volgens de 5S methodiek. Op alle rekken staan duidelijke aanduidingen, die aangeven waar wat moet liggen. Allerlei spullen hebben vaste locaties gekregen om het zoeken te minimaliseren. “Niemand moet meer zoeken”, zegt Olaf Jansen. “Niet naar materialen en producten, maar ook niet meer naar een hamer of een bezem.” Ook is er geschoven met processen. Het plaatmateriaal dat nu binnenkomt kan direct in de opslagrekken worden gelegd. Direct daarnaast staan de lasers. In een aparte ruimte daarnaast staan de ponslasercombinatie en de ontbraammachine. Deze machines worden bediend door vijf mensen: drie operators en twee vaste afruimers, die twee afruimlocaties en een bufferrek tot hun beschikking hebben. Als dat allemaal vol zit, dan stoppen ze met snijden. Olaf Jansen verklaart: “We kijken echt naar het proces en een optimale flow: alle artikelen moeten conform planning op het juiste moment op de volgende plek liggen.”
- Er is ook een moderne klimaatinstallatie geïnstalleerd, die de productieruimte koelt en verwarmt en de lasdampen afzuigt.
- Er is ook een moderne klimaatinstallatie geïnstalleerd, die de productieruimte koelt en verwarmt en de lasdampen afzuigt.
Rust en overzichtelijkheid
Direct achter de lasers staan de kantbanken. Daarna volgen de puntlas- en insertmachines en de aparte lasafdelingen voor staal en RVS die worden gescheiden door een wand. Beide afdelingen zijn op dezelfde manier ingericht zodat de lassers makkelijk hun karretje met spullen kunnen meenemen en op beide plekken kunnen werken. Overal in de productieruimte staan de kenmerkende oranje gekleurde karretjes waarop materialen en onderdelen worden vervoerd. De hele productieruimte straalt rust en overzichtelijkheid uit.
De ruim veertig medewerkers van Made by Driessen zijn continu meegenomen in het verbeterproces en dat werpt nu duidelijk zijn vruchten af. Stefan Driessen: “We hebben bijvoorbeeld twee Kardex systemen aangeschaft voor de opslag van bevestigingsmaterialen. Daar zijn medewerkers zelf mee aan de slag gegaan, ze hebben die kasten zelf ingedeeld. Dat is heel positief opgepakt, iets wat een aantal jaren geleden niet denkbaar was. Het verantwoordelijkheidsgevoel, zelf beslissingen mogen nemen, moest even loskomen maar dat zie je nu gebeuren. De meeste medewerkers pakken het goed op en staan open voor de veranderingen, ze zien de meerwaarde daarvan. Zo krijg je draagvlak.”
Volgende stap
Nu de processen allemaal op orde zijn, is Made by Driessen klaar voor de volgende stap: de processen voor een groot stuk gaan digitaliseren. Hiervoor zal in 2020 een nieuw ERP systeem worden geïmplementeerd, waarmee tevens de basis wordt gelegd voor shopfloorcontrol en een verbeterslag in de planning. Zo blijft Made by Driessen als tweedelijns toeleverancier proactief bezig met het inrichten van haar eigen fabriek van de toekomst. Maar eerst is het tijd voor een feest om stil te staan bij het jubileum en alles wat er al is gerealiseerd. Op 13 december is er van 11.00 tot 16.00 open huis voor iedereen die wil komen kijken. Aansluitend is er ’s avonds een feest voor genodigden en voor het personeel en hun partners. “Dat hebben we allemaal welverdiend”, besluit Stefan Driessen.
Blij en trots
“De samenwerking van Bystronic met Made by Driessen heeft een lange historie die bij de investeringsrondes van de afgelopen jaren verder is versterkt”, zegt Hans van de Meerakker van Bystronic Benelux. “Het is voor ons een genoegen om deel uit te maken van het meerjarenplan dat is uitgerold. Zowel onze automatisering voor het beladen en ontladen van de twee ByStar Fiber lasersnijmachines als de methodiek op de werkvoorbereiding met de offline programmering voor het kanten, paste naadloos aan bij de QRM-wijze van produceren die Made by Driessen voor ogen had. Het is ook fantastisch om te zien dat het vooraf gestelde doel door Made by Driessen wordt bereikt door minutieus stap voor stap alle veranderingen effectief door te voeren. Dat wij als Bystronic daar onderdeel van uitmaken, maakt ons blij en trots want door deze samenwerking is het succes van Made by Driessen ook ons succes.”
Goede referentieklant
“Vanuit SpartnerS ervaar ik de samenwerking met Made by Driessen als positief en professioneel”, aldus Pim van Dorp van SpartnerS Organisatieadvies. “Zo merken we aan de motivatie dat het team van Driessen en van Kempmetal in het gezamenlijke proces graag wil verbeteren. Ook staan de deelnemers altijd open voor nieuwe zienswijzen en gaat men snel met de verbetervoorstellen aan de slag. We zagen dit bijvoorbeeld bij de implementatie van de verbeterde lay-out: het team was van plan om meer liggers in de stellingen te plaatsen. Het nadeel daarvan zou zijn dat er meer ruimte voor tussenvoorraden en onderhanden werk ontstond. Al met al verstorend voor de optimale flow. Gelukkig begrepen de teamleden dit snel, en was daarmee het plan van de baan. Om diezelfde optimale flow te bewaren staat de lasersnijmachine af en toe zelfs stil. Iets waar het team vroeger moeite mee zou hebben: de laser moet toch zoveel mogelijk snijden? Nu ervaart men dat het wegnemen van een bottleneck de flow bevordert en de totale output positief beïnvloedt. Ik merk dat we Made by Driessen graag gebruiken als referentieklant, omdat we trots zijn op wat we samen bereikt hebben! We hopen dat onze mooie samenwerking nog lang door mag blijven gaan.”
- Made by Driessen richt zich helemaal op de productie van hoogwaardige dunne plaatdelen (0,5 tot 2 à 3 mm dik) en het daarbij zoveel mogelijk waarde toevoegen voor de klant.
- Plaatwerktoeleverancier in Eersel sluit ingrijpend verbetertraject af met open huis en jubileumfeest
- Er zijn aparte lasafdelingen voor staal en RVS gecreëerd.