Moeilijk te lassen materiaal printen met EHLA 3D
Kunnen geavanceerde metalen componenten productief en reproduceerbaar in serie 3D geprint worden? Onderzoekers uit Aken kunnen deze vraag bevestigend beantwoorden: bij het Fraunhofer Instituut voor Lasertechnologie ILT hebben ze de tweedimensionale Extreme High-speed Laser Material Deposition (EHLA) overgebracht naar een gemodificeerd vijfassig CNC-systeem voor additive manufacturing van complexe componenten. Door het EHLA-proces uit te breiden naar de derde dimensie, kan het instituut moeilijk te lassen materialen zoals gereedschapsstaal, titanium, aluminium en nikkellegeringen 3D printen.
Snel en nauwkeurig: aan de hand van het voorbeeld van een vormdeel dat additief werd vervaardigd met EHLA 3D, toonde Fraunhofer ILTaan dat het de printtijd aanzienlijk kon verkorten in vergelijking met LMD en LPBF.
Al tientallen jaren domineren twee laserprocessen het printen en coaten van metalen onderdelen. De dominante technologie in direct industrieel, metallic 3D-printen is het op laser gebaseerde poederbedfusieproces (LPBF). Hier smelt de laserstraal een klein deel van het basismateriaal en verandert het poeder in een vaste laag die zich metallurgisch aan het basismateriaal hecht. Zo groeit laag voor laag een 3D-component uit het poederbed.
Efficiënte oppervlaktetechnologie
Laser Material Deposition (LMD) heeft ook bewezen een efficiënte oppervlaktetechnologie van een speciaal soort te zijn. Hierbij wordt een smeltbad gevormd op het oppervlak van het component, waarin het vulmateriaal, draad of poeder continu wordt ingebracht. Deze plas smelt zowel het substraat als het vulmateriaal, wat resulteert in een metallurgische binding tussen de laag en het componentsubstraat.
Het economische potentieel ligt enerzijds in de mogelijkheid om basiscomponenten te upgraden met een functionele laag of om lokale, additieve componentwijzigingen door te voeren. Het tweede belangrijke toepassingsgebied van LMD is de reparatie van dure componenten, bijvoorbeeld uit de lucht- en ruimtevaartindustrie of de gereedschapsmakerij. Versleten of defecte onderdelen kunnen na plaatselijk cladden met LMD weer volledig functioneel worden gemaakt.
Processpecifieke voordelen
LMD en LPBF zijn onmisbaar geworden voor op metaal gebaseerde additive manufacturing, omdat ze processpecifieke voordelen hebben: LMD is aantrekkelijk vanwege de hoge productiviteit, terwijl LPBF kan worden gebruikt voor het 3D-printen van uiterst filigraan en complexe componenten. Fraunhofer ILT en de leerstoel voor digitale additieve productie DAP aan de RWTH Aachen University sloegen in 2012 volledig nieuwe wegen in met de ontwikkeling van Extreme High-speed Laser Material Deposition EHLA. In het gepatenteerde proces smelt een laser de poederdeeltjes al boven het smeltbad. Dankzij deze innovatie kon de processnelheid worden verhoogd van de vorige 0,5 naar 2,0 (LMD) tot maximaal 200 m/min en de laagdikte teruggebracht van 500 naar maximaal 10 µm. Per uur kan nu tot 5 vierkante meter worden gecoat. Daarnaast zijn de coatings gladder geworden.
Succes in snelcoaten
De uitvinding slaat aan: zo heeft Hornet Laser Cladding uit Lexmond een laserstraalbron, EHLA-bewerkingskop en poedertoevoersysteem in haar draaibanken geïntegreerd om EHLA in industriële processen te gebruiken. Trumpf heeft het proces ook opgenomen in zijn productportfolio en biedt laserapparatuur en systeemtechnologieën voor het EHLA-proces. Onder de eerste gebruikers bevinden zich bedrijven in Nederland, China, Duitsland en Turkije. De doorbraak kwam in 2015 voor de offshore-sector: sindsdien zijn vele honderden meters lange hydraulische cilinders gecoat met slijtvaste en corrosiebestendige legeringen voor gebruik in maritieme omgevingen.
In 2019 volgde de stap naar de derde dimensie na verdere successen in het snel en betrouwbaar coaten van remschijven, zuigers, cilinders en lagers. Jonathan Schaible, voormalig onderzoeksmedewerker bij Fraunhofer ILT, behandelde de vraag aan welke speciale eisen voor machine- en systeemtechnologie moet worden voldaan om EHLA te combineren met high-speed 3D-printen. Tegelijkertijd is zijn opvolger, Min-Uh Ko, doorgegaan met het verfijnen van de procesengineering op een speciaal aangepast vijfassig CNC-systeem dat de hoogste precisie verenigt met hoge voedingssnelheden voor additive manufacturing, free-form coating en componentreparatie met behulp van EHLA.
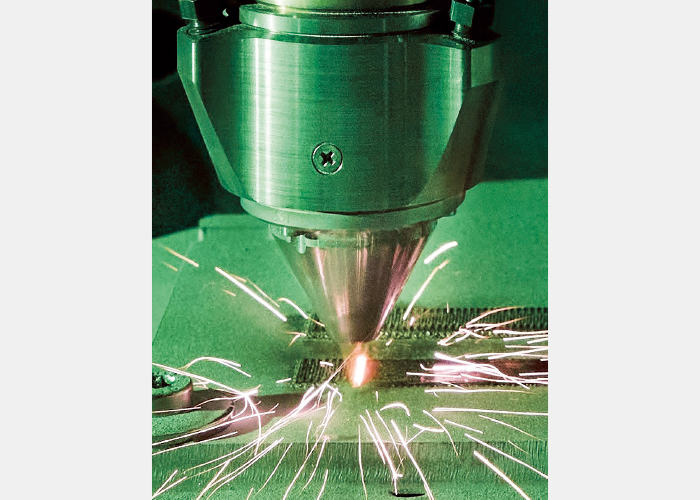
3D-metaalprinten in recordtijd: de voor het EHLA-proces aangepaste CNC-machine kan gereedschappen snel, dynamisch en nauwkeurig in zijwaartse richting verplaatsen. Met een draai- en kanteltafel is hij niet alleen geschikt voor additive manufacturing, maar ook voor oppervlaktecoatings in vrije vorm.
“EHLA 3D combineert de productiviteit van LMD met zijn 500 tot 2000 µm dikke lagen met de structureel gerichte, precieze opbouw van LPBF met 30 tot 100 µm dikke lagen”, legt Ko uit, groepsleider van Additive Manufacturing and Repair LMD bij Fraunhofer ILT. “EHLA 3D zit in het middenbereik met 50 tot 300 µm.”
Dicht bij de uiteindelijke contour
Ook de lage verdunningszone en de hoge koelsnelheid spreken in het voordeel van het proces. Dankzij deze eigenschappen kunnen ook componenten van moeilijk te lassen materialen en combinaties van meerdere materialen additief worden geproduceerd. Het proces toont zijn sterke punten in echt 3D-printen. Ko legt uit: “Met EHLA 3D is het mogelijk productief componenten te vervaardigen die de uiteindelijke contour al dicht benaderen. Naast het zogenaamde near-net shaping, maakt het proces het ook mogelijk om snel en precies te bouwen, maar ook om coatings aan te brengen op vrije-vorm oppervlakken.”
EHLA 3D maakt complexe vormen in recordtijd mogelijk. Wetenschapper Ko liet op een congres in Aken al eens een video zien, die de productieve, additive manufacturing demonstreert van een vormgereedschap waarvan de afdruktijd met een factor twee kon worden verkort in vergelijking met LMD. Bovendien ontstaan nog meer voordelen door de vermindering van de inspanning die nodig is voor de afwerkingsbewerking.
Met gebruikt poeder
Het proces kent ook een hoge efficiëntie: componenten gemaakt van het ruimtevaartmateriaal Inconel 718 werden 3D-geprint op het vijfassige CNC-systeem met een depositiesnelheid van meer dan 2 kg/u met een dichtheid van meer dan 99,5 procent. De onderzoekers uit Aken onderzochten ook hoe de karakteristieke waarden veranderen als ze werken met gerecycled metaalpoeder in plaats van nieuw. In beide gevallen lag de treksterkte Rm rond de 1300 MPa. Ko legt uit: “In beide gevallen bleek de treksterkte net zo goed te zijn als bij gieten.” Goede resultaten behaalde ook wetenschapper Schaible, wiens werk onder meer de EHLA 3D-procesontwikkeling van componenten gemaakt van 316L roestvrij staal en aluminium-siliciumlegeringen omvatte. Ook hier zijn de verkregen mechanische eigenschappen in overeenstemming met die vermeld in de literatuur voor conventioneel geproduceerde monsters. De momenteel mogelijke structurele resolutie van dunwandige aluminium componenten geproduceerd met EHLA 3D is ongeveer 500 µm.